易卖工控网(www.ymgk.com)提供”AVME9675-2-501837模块备件”,产品详情:品牌/厂家:0040-32460-504815、型号:AVME9675-2-501837、成色:全新、货期:现货 1天内发货、保修:180天,更多产品详情就上易卖工控网。
Agilent Technologies-501836 直接转矩控制(DTC)是先进的交流传动装置 世界上任何制造商开发的技术。 本技术指南的目的 本技术指南的目的是解释什么是DTC; 为什么以及如何演变;其成功背后的基本理论; 以及这项新技术的特点和点。 虽然本指南尽量实用,但它确实需要 对交流电机控制原理有基本了解。 它针对的是决策者,包括设计师、说明符、, 采购经理、原始设备制造商和终用户;在所有市场中 如水、化工、制浆造纸、发电、物料搬运、空调等行业。 事实上,任何使用变速驱动器(VSD)的人以及 想从VSD技术中获益,请参阅本技术指南 基本阅读。 使用本指南 本指南旨在对以下方面进行逻辑构建: 为什么以及如何开发DTC。 读者希望了解早期直流电驱动器的演变 从交流到DTC的技术应从2章(8页)开始。 对于那些想了解DTC性能的读者, 操作和应用潜力,请直接进入章 3(17页)问答。 要了解DTC的基本控制理论,请转至 28页。 8直接转矩控制|技术指南1 2章-直接转矩的演变 控制 什么是变速驱动? 要理解这个问题的答案,我们必须理解 变速驱动器(VSD)的基本功能是控制 从电源到过程的能量流。 能量通过电机轴提供给过程。二 物理量描述轴的状态:扭矩和 速度因此,为了控制能量的流动,我们终必须, 控制这些数量。 实际上,它们中的任何一个都是受控的,我们所说的 “扭矩控制”或“速度控制”。VSD运行时 在扭矩控制模式下,速度由负载决定。 同样,当在速度控制中操作时,扭矩由负载决定。 初,直流电机被用作VSD,因为它们可以轻松实现所需的速度和扭矩,而无需 密电子设备。 然而,交流变速驱动技术的发展 部分原因是想效仿秀人才 直流电机的性能,例如快速转矩响应和 速度度高,同时使用坚固、廉价且免维护的交流电机。 总结 在本节中,我们将介绍DTC的发展,并绘制四个 变速驱动的里程碑,即: –直流电机驱动9 –交流驱动、频率控制、PWM 11 –交流驱动、磁通矢量控制、PWM 12 –交流驱动,直接转矩控制14 我们依次检查每一个,得出一个确定 它们之间的关键区别。 技术指南1 |直接转矩控制9 1. 直接转矩控制的发展 直流电机驱动 图1:直流电机驱动器的控制回路 特征 –通过机械换向器的磁场定向 –控制变量为电枢电流和励磁电流, 直接从电机测量 –扭矩控制是直接的 在直流电机中,磁场是通过电流产生的 定子中的励磁绕组。该字段始终与 电枢绕组产生的磁场。这种情况,已知 作为磁场定向,需要产生大扭矩。这个 换向器电刷组件确保保持这种状态 无论转子位置如何。 一旦实现磁场定向,直流电机的转矩很容易 通过改变电枢电流和保持 磁化电流常数。 直流驱动器的点是速度和扭矩 终用户的主要关注点-直接通过 电枢电流:即转矩是内部控制回路和 速度是外部控制回路(见图1)。 势 –确快速的扭矩控制 –高动态速度响应 –易于控制 初,直流驱动器用于变速控制,因为 它们可以轻松实现良好的扭矩和速度响应 具有高度。 10直接转矩控制|技术指南1 直流电机能够产生以下扭矩: –直接-电机扭矩与臂成比例 电流:因此可以直接控制扭矩 准确。 –快速-扭矩控制快速;驱动系统可以具有 非常高的动态速度响应。扭矩可以是 如果电机由理想电源供电,则瞬时改变 电流源。电压馈电驱动器仍然具有快速 响应,因为这仅由转子的 电时间常数(即总电感和 电枢电路中的电阻) –Simple-使用简单的 称为换向器/电刷组件的机械装置。 因此,不需要复杂的电子控制 电路,我会 Agilent Technologies-501836 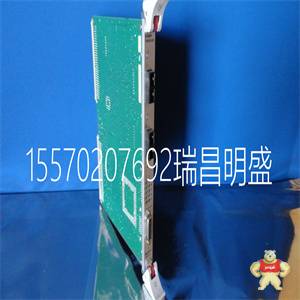 Agilent Technologies-501836 | | |
Direct torque control - or DTC - is the most advanced AC drive technology developed by any manufacturer in the world. This technical guide’s purpose The purpose of this technical guide is to explain what DTC is; why and how it has evolved; the basic theory behind its success; and the features and benefits of this new technology. While trying to be as practical as possible, this guide does require a basic understanding of AC motor control principles. It is aimed at decision makers including designers, specifiers, purchasing managers, OEMs and end-users; in all markets such as the water, chemical, pulp and paper, power generation, material handling, air conditioning and other industries. In fact, anyone using variable speed drives (VSD) and who would like to benefit from VSD technology will find this technical guide essential reading. Using this guide This guide has been designed to give a logical build up as to why and how DTC was developed. Readers wanting to know the evolution of drives from early DC techniques through AC to DTC should start at chapter 2 (page 8). For those readers wanting answers about DTC’s performance, operation and application potential, please go straight to chapter 3 (page 17) Questions and answers. For an understanding of DTC’s basic control theory, turn to page 28. 8 Direct torque control | Technical guide No. 1 Chapter 2 - Evolution of direct torque control What is a variable speed drive? To understand the answer to this question we have to understand that the basic function of a variable speed drive (VSD) is to control the flow of energy from the mains to the process. Energy is supplied to the process through the motor shaft. Two physical quantities describe the state of the shaft: torque and speed. To control the flow of energy we must therefore, ultimately, control these quantities. In practice, either one of them is controlled and we speak of “torque control” or “speed control”. When the VSD operates in torque control mode, the speed is determined by the load. Likewise, when operated in speed control, the torque is determined by the load. Initially, DC motors were used as VSDs because they could easily achieve the required speed and torque without the need for sophisticated electronics. However, the evolution of AC variable speed drive technology has been driven partly by the desire to emulate the excellent performance of the DC motor, such as fast torque response and speed accuracy, while using rugged, inexpensive and maintenance free AC motors. Summary In this section we look at the evolution of DTC, charting the four milestones of variable speed drives, namely: – DC motor drives 9 – AC drives, frequency control, PWM 11 – AC drives, flux vector control, PWM 12 – AC drives, direct torque control 14 We examine each in turn, leading to a total picture that identifies the key differences between each. Technical guide No. 1 | Direct torque control 9 1 Evolution of direct torque control DC motor drives Figure 1: Control loop of a DC motor drive Features – Field orientation via mechanical commutator – Controlling variables are armature current and field current, measured DIRECTLY from the motor – Torque control is direct In a DC motor, the magnetic field is created by the current through the field winding in the stator. This field is always at right angles to the field created by the armature winding. This condition, known as field orientation, is needed to generate maximum torque. The commutator-brush assembly ensures this condition is maintained regardless of the rotor position. Once field orientation is achieved, the DC motor’s torque is easily controlled by varying the armature current and by keeping the magnetising current constant. The advantage of DC drives is that speed and torque - the two main concerns of the end-user - are controlled directly through armature current: that is the torque is the inner control loop and the speed is the outer control loop (see Figure 1). Advantages – Accurate and fast torque control – High dynamic speed response – Simple to control Initially, DC drives were used for variable speed control because they could easily achieve a good torque and speed response with high accuracy. 10 Direct torque control | Technical guide No. 1 A DC machine is able to produce a torque that is: – Direct - the motor torque is proportional to the armture current: the torque can thus be controlled directly and accurately. – Rapid - torque control is fast; the drive system can have a very high dynamic speed response. Torque can be changed instantaneously if the motor is fed from an ideal current source. A voltage fed drive still has a fast response, since this is determined only by the rotor’s electrical time constant (ie, the total inductance and resistance in the armature circuit) – Simple - field orientation is achieved using a simple mechanical device called a commutator/brush assembly. Hence, there is no need for complex electronic control circuitry, which would increase the cost of the motor controller. Drawbacks – Reduced motor reliability – Regular maintenance – Motor costly to purchase – Needs encoder for feedback The main drawback of this technique is the reduced reliability of the DC motor; the fact that brushes and commutators wear down and need regular servicing; that DC motors can be costly to purchase; and that they require encoders for speed and position feedback. While a DC drive produces an easily controlled torque from zero to base speed and beyond, the motor’s mechanics are more complex and require regular maintenance. AC drives - Introduction – Small size – Robust – Simple in design – Light and compact – Low maintenance – Low cost The evolution of AC variable speed drive technology has been partly driven by the desire to emulate the performance of the DC drive, such as fast torque response and speed accuracy, while utilising the advantages offered by the standard AC motor. Evolution of direct torque control Technical guide No. 1 | Direct torque control 11 1 AC drives -Frequency control using PWM Figure 2: Control loop of an AC drive with frequency control using PWM Features – Controlling variables are voltage and frequency – Simulation of variable AC sine wave using modulator – Flux provided with constant V/f ratio – Open-loop drive – Load dictates torque level Unlike a DC drive, the AC drive frequency control technique uses parameters generated outside of the motor as controlling variables, namely voltage and frequency. Both voltage and frequency reference are fed into a modulator which simulates an AC sine wave and feeds this to the motor’s stator windings. This technique is called pulse width modulation (PWM) and utilises the fact that there is a diode rectifier towards the mains and the intermediate DC voltage is kept constant. The inverter controls the motor in the form of a PWM pulse train dictating both the voltage and frequency. Significantly, this method does not use a feedback device which takes speed or position measurements from the motor’s shaft and feeds these back into the control loop. Such an arrangement, without a feedback device, is called an “open-loop drive”. Evolution of direct torque control 12 Direct torque control | Technical guide No. 1 Advantages – Low cost – No feedback device required - simple Because there is no feedback device, the controlling principle offers a low cost and simple solution to controlling economical AC induction motors. This type of drive is suitable for applications which do not require high levels of accuracy or precision, such as pumps and fans. Drawbacks – Field orientation not used – Motor status ignored – Torque is not controlled – Delaying modulator used With this technique, sometimes known as scalar control, field orientation of the motor is not used. Instead, frequency and voltage are the main control variables and are applied to the stator windings. The status of the rotor is ignored, meaning that no speed or position signal is fed back. Therefore, torque cannot be controlled with any degree of accuracy. Furthermore, the technique uses a modulator which basically slows down communication between the incoming voltage and frequency signals and the need for the motor to respond to this changing signal. AC drives - Flux vector control using PWM Figure 3: Control loop of an AC drive with flux vector control using PWM Features – Field-oriented control - simulates DC drive – Motor electrical characteristics are simulated - “ motor model” – Closed-loop drive – Torque controlled INDIRECTLY
易卖工控网供应商瑞昌明盛进出口贸易有限公司为您提供AVME9675-2-501837模块备件的详细产品价格、产品图片等产品介绍信息,您可以直接联系商家获取AVME9675-2-501837模块备件的具体资料,联系时请说明是在易卖工控网看到的。